-
Precision Machining
Dive into perfection with our precision machining capabilities, offering unparalleled accuracy for components that demand strict adherence to specifications. With cutting-edge technology, we transform the most robust materials into intricate parts designed for performance
-
Metal Stamping
Experience efficiency and strength with our metal stamping services. From simple designs to complex geometries, our presses and strategic processes handle diverse requirements, producing high-volume parts without sacrificing precision
-
Aluminum Extrusion
Explore versatility with our aluminum extrusion capabilities. Leveraging advanced techniques, we shape aluminum into definitive components, achieving complex cross-sectional profiles that meet rigorous industry demands
-
Casting Solutions
Uncover the full spectrum of our casting prowess. Whether it’s through sand casting, die casting, or investment casting, we craft components with meticulous attention to detail, ensuring structural integrity and functional precision
Promax Engineering Capabilities
Expertise Fueling Diverse Industrial Triumphs
Navigating through over two decades of transformative innovation, Promax Engineering stands as a beacon of excellence in manufacturing, crafting its legacy across automotive, appliance, and special vehicle industries. Our journey is marked by relentless dedication, evolving capabilities, and a robust portfolio that accentuates our proficiency in producing paramount metal parts. Each component we engineer is a testament to our versatile expertise, reflecting the depth of service and innovation we bring to every industry we serve.
Our Prowess:
Precision machining is a sophisticated process that removes excess raw material from a work-piece, while holding close tolerance finishes, to create detailed parts with highly accurate dimensions. It encompasses various techniques including milling, turning, drilling, and electrical discharge machining, among others. Promax Engineering leverages advanced technology and a refined approach to transform sturdy materials into complex parts defined by precision.
-
Unmatched Accuracy: By adhering to stringent tolerances, precision machining ensures components are manufactured with supreme accuracy, crucial in applications where perfection cannot be compromised.
-
Consistency at Scale: Whether for single prototypes or high-volume production, the process delivers consistent results, maintaining quality across batches, essential for large-scale industrial applications.
-
Material Versatility: From metals to plastics, precision machining can handle a diverse range of materials, accommodating various industrial requirements for component manufacturing.
-
Complexity Simplified: This technique supports the creation of complex, intricate parts that might be impossible to produce through traditional manufacturing methods, thereby broadening design possibilities.
-
CNC Mills: Computer-controlled milling machines provide unparalleled precision and flexibility in producing parts with complex geometries.
-
CNC Lathes: These machines perform turning operations with extreme accuracy, creating detailed external and internal geometries on work-pieces.
-
Electrical Discharge Machines (EDM): EDMs are essential for shaping hard metals or those that would be impossible to machine with traditional techniques.
-
Grinding Machines: Ideal for finishing surfaces, these machines provide high precision in terms of dimensional accuracy and shape, delivering superior surface quality.
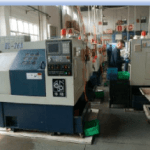
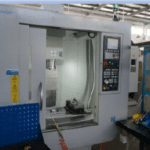
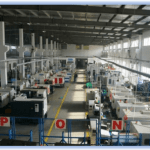
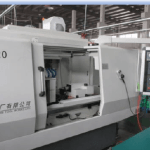
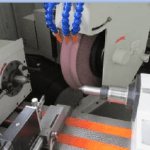
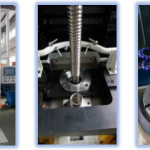
-
Automotive: Precision machining is critical in creating components, from engines to ancillary parts, that meet the exacting standards of the automotive industry.
-
Appliance: Household and commercial appliances rely on high-precision parts for operational efficiency and durability, ensuring reliability and user safety.
-
Special Vehicles: Custom vehicles, including emergency services, military, or recreational vehicles, require unique, often complex components manufactured through precision machining for enhanced performance and reliability.
-
Aerospace: The aerospace industry demands components with a high strength-to-weight ratio, manufactured to the most exacting specifications for optimal performance and safety.
At Promax Engineering, precision is not just a process; it’s a promise. Our cutting-edge technology, coupled with our deep industry knowledge, ensures that the components we produce set new benchmarks in quality and precision, driving the success of industries we serve. Our meticulous attention to detail champions the essence of true craftsmanship, powering innovation across diverse sectors.
Metal stamping is a highly versatile manufacturing process used to convert flat metal sheets into specific shapes. It involves a series of high-precision procedures such as punching, blanking, embossing, bending, flanging, and coining, using a stamping press or stamping machines. At Promax Engineering, we specialize in transforming sheets of metal into high-strength parts that contribute to the backbone of various industries.
- Efficiency and Speed: Metal stamping machines can produce a high volume of complex parts quickly, making the process ideal for mass production.
- Cost-Effectiveness: Due to its suitability for high-volume production, metal stamping is a cost-efficient process, significantly reducing the per-unit cost of components.
- High Precision: Advanced stamping techniques ensure each part adheres to stringent specifications, contributing to the overall quality and functionality of the final product.
- Versatility: From simple to complex designs, metal stamping accommodates a wide range of shapes and sizes, serving diverse manufacturing needs.
- Mechanical Presses: Known for speed and accuracy, mechanical presses are used for a broad array of stamping applications, utilizing fixed strokes and speeds.
- Hydraulic Presses: These machines offer flexibility with adjustable stroke lengths, allowing for deeper draws and a wider range of operations.
- Servo Presses: With programmable stroke lengths, speeds, and pressures, servo presses provide greater control and energy efficiency, perfect for more complex or precision-heavy stamping requirements.
- Progressive Die Stamping Machines: These are used for producing high-volume, intricate parts, significantly reducing costs and boosting production rates.
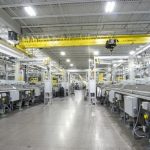
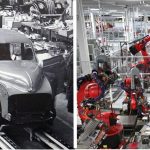
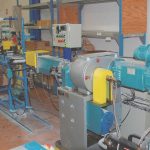
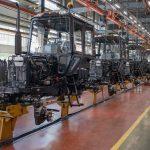
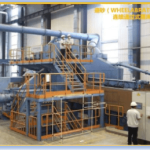
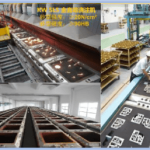
Automotive: Metal stamping is integral in manufacturing various automotive parts, contributing to the vehicles’ structure, aesthetics, and functionality.
Appliance: For both domestic and commercial appliances, metal stamping provides the essential components that enhance the durability and performance of the products.
Special Vehicles: This sector requires bespoke components that meet specific standards, and metal stamping allows for the customization needed for these specialized units.
Electronics: The electronics industry utilizes metal stamping for creating precise components that form the integral parts of devices and circuit boards.
In the realm of metal stamping, Promax Engineering is synonymous with excellence. Our facilities are equipped with state-of-the-art machinery that brings precision, efficiency, and quality to every stage of the manufacturing process. We serve as the trusted backbone for industries, ensuring that they receive components that pass the highest standards of strength, durability, and precision. With us, every stamped metal part signifies a promise of quality and reliability.
Aluminum extrusion is a transformative manufacturing technique where aluminum alloy is forced through a shaped opening in a die, creating a specific cross-sectional profile. The extruded material emerges as an elongated piece with the same profile as the die opening. At Promax Engineering, we utilize this method to produce a diverse array of components, offering a combination of lightweight flexibility and robust strength for various applications.
-
Design Flexibility: Aluminum extrusion allows for complex shapes with a high level of intricacy, accommodating innovative designs and custom applications.
-
Strength & Durability: The process enhances the natural strength of aluminum, resulting in parts that are both strong and resilient, suitable for various environments and purposes.
-
Cost-Efficiency: Aluminum extrusion is economical, particularly for high-volume production, as it allows for rapid, repeatable manufacturing, reducing overall production costs.
-
Seamless Integration: Extruded parts can be designed to snap or fit together with other components, facilitating easier assembly processes and reducing secondary operation costs.
-
Hydraulic Extrusion Presses: These machines can generate a tremendous amount of force, allowing the creation of complex and intricate cross-sections in extruded profiles.
-
Direct / Indirect Extrusion Presses: Depending on the specific requirements of the task, these presses can handle varied extrusion processes, offering both standard and reverse extrusion capabilities.
-
Aging Ovens: These are used post-extrusion to accelerate the aging process of aluminum, enhancing its final properties through controlled heat treatment.
-
Precision Cutters: For ensuring exact length specifications, precision cutting tools are employed, providing uniformity across batches.
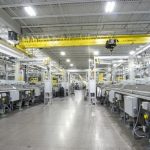
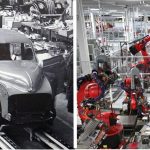
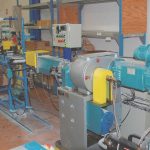
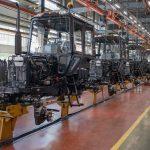
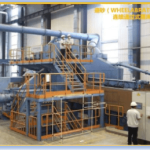
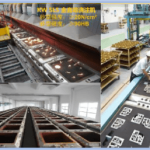
-
Automotive: Aluminum extrusion is vital for creating lightweight, durable components for vehicles, contributing to fuel efficiency and overall performance.
-
Construction: In construction, extruded aluminum profiles are used for structural and design elements, offering durability and resistance to environmental factors.
-
Aerospace: The aerospace industry values extruded aluminum for its strength-to-weight ratio, corrosion resistance, and suitability for complex shapes.
-
Electronics: Thanks to its thermal conductivity and shielding properties, extruded aluminum is widely used in electronic housings and components.
At Promax Engineering, we steer the future of advanced aluminum extrusions with our cutting-edge technology and seasoned expertise. Our dedication lies in meeting precise client specifications with every component, ensuring consistency, durability, and superior quality. By merging technical prowess with relentless innovation, we shape solutions that propel industries forward, marking us as a forerunner in aluminum extrusion services.
Casting is a manufacturing process where a liquid material is poured into a mold containing a hollow cavity of the desired shape, then allowed to solidify. The solidified part, known as a casting, is then ejected or broken out to complete the process. At Promax Engineering, we offer a range of casting methods — including die, sand, and investment casting — to create parts that meet diverse and complex industrial needs.
-
Design Versatility: Casting accommodates complex shapes and designs, including internal cavities and intricacies that would be difficult to achieve with other manufacturing processes.
-
Size Flexibility: The process supports a broad size range, capable of producing tiny components for intricate applications or large parts for heavy-duty uses.
-
Cost-Efficiency: Casting is often more economical for creating complex shapes because it requires fewer secondary machining and fabrication processes. It’s particularly cost-effective for high-volume production.
-
Material Choice: A wide range of metals and materials can be used in the casting process, allowing for specific material properties like durability, strength, and temperature resistance.
-
Furnaces: Used for melting and maintaining molten material before it is poured into molds.
-
Die Casting Machines: These are used for forcing molten metal into molds under high pressure, ideal for high-volume, consistent production runs.
-
Molding Machines for Sand Casting: These prepare the sand molds into which molten metal is poured, used for casting complex shapes.
-
Centrifugal Casting Machines: They use centrifugal force to produce cylindrical parts with a great finish and high material integrity.
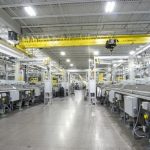
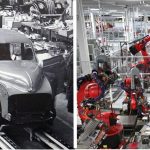
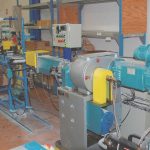
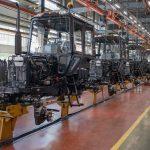
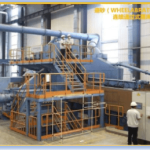
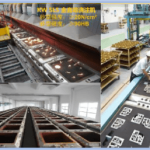
-
Automotive: Casting creates durable, complex components for vehicles, including engine parts, pump housings, and more, contributing to the efficiency and reliability of automotive assemblies.
-
Aerospace: The aerospace industry requires high-strength, precision-made components, often achieved through casting processes to handle extreme conditions effectively.
-
Heavy Machinery: Casting is used to create robust parts for machinery in construction, mining, and other heavy-duty industrial applications, demanding high performance and durability.
-
Consumer Electronics: Precise and aesthetic components for gadgets and consumer electronics are often manufactured using specialized casting methods for detailed design realization.
Promax Engineering takes pride in its sophisticated casting solutions, offering unmatched expertise and technological advances to meet complex industry demands. Our comprehensive casting services are a testament to our commitment to quality, precision, and customer satisfaction. We ensure each cast component adheres to the highest standards, enhancing the operational integrity of the applications they serve, and driving progress across various industries.
Precision machining is a sophisticated process that removes excess raw material from a work-piece, while holding close tolerance finishes, to create detailed parts with highly accurate dimensions. It encompasses various techniques including milling, turning, drilling, and electrical discharge machining, among others. Promax Engineering leverages advanced technology and a refined approach to transform sturdy materials into complex parts defined by precision.
-
Unmatched Accuracy: By adhering to stringent tolerances, precision machining ensures components are manufactured with supreme accuracy, crucial in applications where perfection cannot be compromised.
-
Consistency at Scale: Whether for single prototypes or high-volume production, the process delivers consistent results, maintaining quality across batches, essential for large-scale industrial applications.
-
Material Versatility: From metals to plastics, precision machining can handle a diverse range of materials, accommodating various industrial requirements for component manufacturing.
-
Complexity Simplified: This technique supports the creation of complex, intricate parts that might be impossible to produce through traditional manufacturing methods, thereby broadening design possibilities.
-
CNC Mills: Computer-controlled milling machines provide unparalleled precision and flexibility in producing parts with complex geometries.
-
CNC Lathes: These machines perform turning operations with extreme accuracy, creating detailed external and internal geometries on work-pieces.
-
Electrical Discharge Machines (EDM): EDMs are essential for shaping hard metals or those that would be impossible to machine with traditional techniques.
-
Grinding Machines: Ideal for finishing surfaces, these machines provide high precision in terms of dimensional accuracy and shape, delivering superior surface quality.
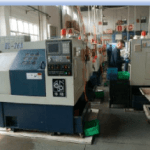
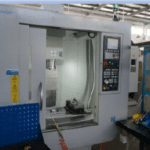
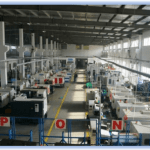
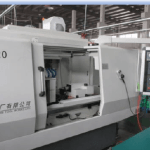
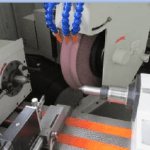
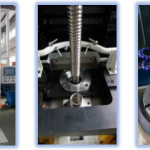
-
Automotive: Precision machining is critical in creating components, from engines to ancillary parts, that meet the exacting standards of the automotive industry.
-
Appliance: Household and commercial appliances rely on high-precision parts for operational efficiency and durability, ensuring reliability and user safety.
-
Special Vehicles: Custom vehicles, including emergency services, military, or recreational vehicles, require unique, often complex components manufactured through precision machining for enhanced performance and reliability.
-
Aerospace: The aerospace industry demands components with a high strength-to-weight ratio, manufactured to the most exacting specifications for optimal performance and safety.
At Promax Engineering, precision is not just a process; it’s a promise. Our cutting-edge technology, coupled with our deep industry knowledge, ensures that the components we produce set new benchmarks in quality and precision, driving the success of industries we serve. Our meticulous attention to detail champions the essence of true craftsmanship, powering innovation across diverse sectors.
Precision machining is a sophisticated process that removes excess raw material from a work-piece, while holding close tolerance finishes, to create detailed parts with highly accurate dimensions. It encompasses various techniques including milling, turning, drilling, and electrical discharge machining, among others. Promax Engineering leverages advanced technology and a refined approach to transform sturdy materials into complex parts defined by precision.
https://wp.promaxeng.com/wp-content/uploads/promax-1-convert.mp4
-
Unmatched Accuracy: By adhering to stringent tolerances, precision machining ensures components are manufactured with supreme accuracy, crucial in applications where perfection cannot be compromised.
-
Consistency at Scale: Whether for single prototypes or high-volume production, the process delivers consistent results, maintaining quality across batches, essential for large-scale industrial applications.
-
Material Versatility: From metals to plastics, precision machining can handle a diverse range of materials, accommodating various industrial requirements for component manufacturing.
-
Complexity Simplified: This technique supports the creation of complex, intricate parts that might be impossible to produce through traditional manufacturing methods, thereby broadening design possibilities.
-
CNC Mills: Computer-controlled milling machines provide unparalleled precision and flexibility in producing parts with complex geometries.
-
CNC Lathes: These machines perform turning operations with extreme accuracy, creating detailed external and internal geometries on work-pieces.
-
Electrical Discharge Machines (EDM): EDMs are essential for shaping hard metals or those that would be impossible to machine with traditional techniques.
-
Grinding Machines: Ideal for finishing surfaces, these machines provide high precision in terms of dimensional accuracy and shape, delivering superior surface quality.
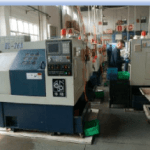
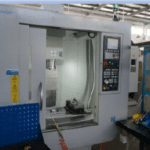
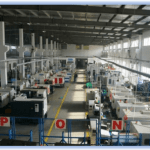
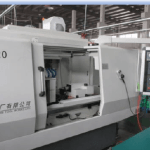
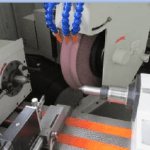
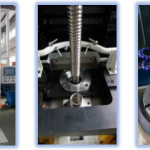
-
Automotive: Precision machining is critical in creating components, from engines to ancillary parts, that meet the exacting standards of the automotive industry.
-
Appliance: Household and commercial appliances rely on high-precision parts for operational efficiency and durability, ensuring reliability and user safety.
-
Special Vehicles: Custom vehicles, including emergency services, military, or recreational vehicles, require unique, often complex components manufactured through precision machining for enhanced performance and reliability.
-
Aerospace: The aerospace industry demands components with a high strength-to-weight ratio, manufactured to the most exacting specifications for optimal performance and safety.
At Promax Engineering, precision is not just a process; it’s a promise. Our cutting-edge technology, coupled with our deep industry knowledge, ensures that the components we produce set new benchmarks in quality and precision, driving the success of industries we serve. Our meticulous attention to detail champions the essence of true craftsmanship, powering innovation across diverse sectors.
Metal stamping is a highly versatile manufacturing process used to convert flat metal sheets into specific shapes. It involves a series of high-precision procedures such as punching, blanking, embossing, bending, flanging, and coining, using a stamping press or stamping machines. At Promax Engineering, we specialize in transforming sheets of metal into high-strength parts that contribute to the backbone of various industries.
- Efficiency and Speed: Metal stamping machines can produce a high volume of complex parts quickly, making the process ideal for mass production.
- Cost-Effectiveness: Due to its suitability for high-volume production, metal stamping is a cost-efficient process, significantly reducing the per-unit cost of components.
- High Precision: Advanced stamping techniques ensure each part adheres to stringent specifications, contributing to the overall quality and functionality of the final product.
- Versatility: From simple to complex designs, metal stamping accommodates a wide range of shapes and sizes, serving diverse manufacturing needs.
- Mechanical Presses: Known for speed and accuracy, mechanical presses are used for a broad array of stamping applications, utilizing fixed strokes and speeds.
- Hydraulic Presses: These machines offer flexibility with adjustable stroke lengths, allowing for deeper draws and a wider range of operations.
- Servo Presses: With programmable stroke lengths, speeds, and pressures, servo presses provide greater control and energy efficiency, perfect for more complex or precision-heavy stamping requirements.
- Progressive Die Stamping Machines: These are used for producing high-volume, intricate parts, significantly reducing costs and boosting production rates.
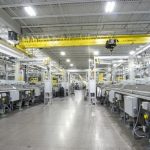
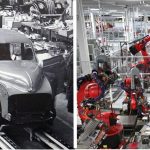
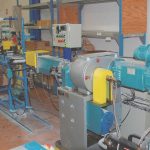
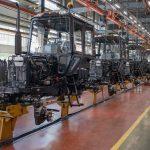
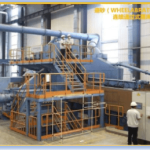
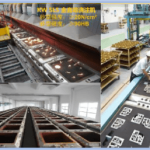
Automotive: Metal stamping is integral in manufacturing various automotive parts, contributing to the vehicles’ structure, aesthetics, and functionality.
Appliance: For both domestic and commercial appliances, metal stamping provides the essential components that enhance the durability and performance of the products.
Special Vehicles: This sector requires bespoke components that meet specific standards, and metal stamping allows for the customization needed for these specialized units.
Electronics: The electronics industry utilizes metal stamping for creating precise components that form the integral parts of devices and circuit boards.
In the realm of metal stamping, Promax Engineering is synonymous with excellence. Our facilities are equipped with state-of-the-art machinery that brings precision, efficiency, and quality to every stage of the manufacturing process. We serve as the trusted backbone for industries, ensuring that they receive components that pass the highest standards of strength, durability, and precision. With us, every stamped metal part signifies a promise of quality and reliability.
Metal stamping is a highly versatile manufacturing process used to convert flat metal sheets into specific shapes. It involves a series of high-precision procedures such as punching, blanking, embossing, bending, flanging, and coining, using a stamping press or stamping machines. At Promax Engineering, we specialize in transforming sheets of metal into high-strength parts that contribute to the backbone of various industries.
https://wp.promaxeng.com/wp-content/uploads/promax-1-convert.mp4
- Efficiency and Speed: Metal stamping machines can produce a high volume of complex parts quickly, making the process ideal for mass production.
- Cost-Effectiveness: Due to its suitability for high-volume production, metal stamping is a cost-efficient process, significantly reducing the per-unit cost of components.
- High Precision: Advanced stamping techniques ensure each part adheres to stringent specifications, contributing to the overall quality and functionality of the final product.
- Versatility: From simple to complex designs, metal stamping accommodates a wide range of shapes and sizes, serving diverse manufacturing needs.
- Mechanical Presses: Known for speed and accuracy, mechanical presses are used for a broad array of stamping applications, utilizing fixed strokes and speeds.
- Hydraulic Presses: These machines offer flexibility with adjustable stroke lengths, allowing for deeper draws and a wider range of operations.
- Servo Presses: With programmable stroke lengths, speeds, and pressures, servo presses provide greater control and energy efficiency, perfect for more complex or precision-heavy stamping requirements.
- Progressive Die Stamping Machines: These are used for producing high-volume, intricate parts, significantly reducing costs and boosting production rates.
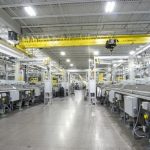
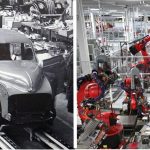
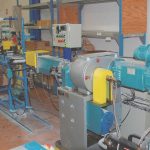
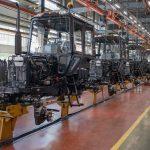
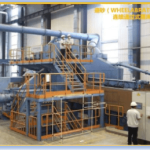
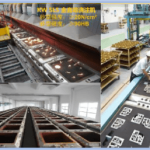
Automotive: Metal stamping is integral in manufacturing various automotive parts, contributing to the vehicles’ structure, aesthetics, and functionality.
Appliance: For both domestic and commercial appliances, metal stamping provides the essential components that enhance the durability and performance of the products.
Special Vehicles: This sector requires bespoke components that meet specific standards, and metal stamping allows for the customization needed for these specialized units.
Electronics: The electronics industry utilizes metal stamping for creating precise components that form the integral parts of devices and circuit boards.
In the realm of metal stamping, Promax Engineering is synonymous with excellence. Our facilities are equipped with state-of-the-art machinery that brings precision, efficiency, and quality to every stage of the manufacturing process. We serve as the trusted backbone for industries, ensuring that they receive components that pass the highest standards of strength, durability, and precision. With us, every stamped metal part signifies a promise of quality and reliability.
Aluminum extrusion is a transformative manufacturing technique where aluminum alloy is forced through a shaped opening in a die, creating a specific cross-sectional profile. The extruded material emerges as an elongated piece with the same profile as the die opening. At Promax Engineering, we utilize this method to produce a diverse array of components, offering a combination of lightweight flexibility and robust strength for various applications.
-
Design Flexibility: Aluminum extrusion allows for complex shapes with a high level of intricacy, accommodating innovative designs and custom applications.
-
Strength & Durability: The process enhances the natural strength of aluminum, resulting in parts that are both strong and resilient, suitable for various environments and purposes.
-
Cost-Efficiency: Aluminum extrusion is economical, particularly for high-volume production, as it allows for rapid, repeatable manufacturing, reducing overall production costs.
-
Seamless Integration: Extruded parts can be designed to snap or fit together with other components, facilitating easier assembly processes and reducing secondary operation costs.
-
Hydraulic Extrusion Presses: These machines can generate a tremendous amount of force, allowing the creation of complex and intricate cross-sections in extruded profiles.
-
Direct / Indirect Extrusion Presses: Depending on the specific requirements of the task, these presses can handle varied extrusion processes, offering both standard and reverse extrusion capabilities.
-
Aging Ovens: These are used post-extrusion to accelerate the aging process of aluminum, enhancing its final properties through controlled heat treatment.
-
Precision Cutters: For ensuring exact length specifications, precision cutting tools are employed, providing uniformity across batches.
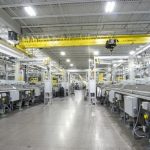
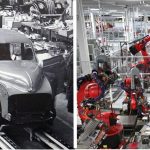
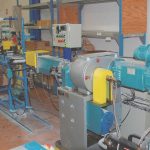
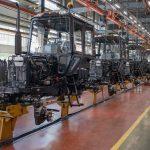
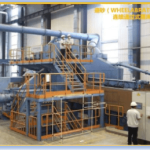
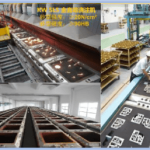
-
Automotive: Aluminum extrusion is vital for creating lightweight, durable components for vehicles, contributing to fuel efficiency and overall performance.
-
Construction: In construction, extruded aluminum profiles are used for structural and design elements, offering durability and resistance to environmental factors.
-
Aerospace: The aerospace industry values extruded aluminum for its strength-to-weight ratio, corrosion resistance, and suitability for complex shapes.
-
Electronics: Thanks to its thermal conductivity and shielding properties, extruded aluminum is widely used in electronic housings and components.
At Promax Engineering, we steer the future of advanced aluminum extrusions with our cutting-edge technology and seasoned expertise. Our dedication lies in meeting precise client specifications with every component, ensuring consistency, durability, and superior quality. By merging technical prowess with relentless innovation, we shape solutions that propel industries forward, marking us as a forerunner in aluminum extrusion services.
Aluminum extrusion is a transformative manufacturing technique where aluminum alloy is forced through a shaped opening in a die, creating a specific cross-sectional profile. The extruded material emerges as an elongated piece with the same profile as the die opening. At Promax Engineering, we utilize this method to produce a diverse array of components, offering a combination of lightweight flexibility and robust strength for various applications.
https://wp.promaxeng.com/wp-content/uploads/promax-1-convert.mp4
-
Design Flexibility: Aluminum extrusion allows for complex shapes with a high level of intricacy, accommodating innovative designs and custom applications.
-
Strength & Durability: The process enhances the natural strength of aluminum, resulting in parts that are both strong and resilient, suitable for various environments and purposes.
-
Cost-Efficiency: Aluminum extrusion is economical, particularly for high-volume production, as it allows for rapid, repeatable manufacturing, reducing overall production costs.
-
Seamless Integration: Extruded parts can be designed to snap or fit together with other components, facilitating easier assembly processes and reducing secondary operation costs.
-
Hydraulic Extrusion Presses: These machines can generate a tremendous amount of force, allowing the creation of complex and intricate cross-sections in extruded profiles.
-
Direct / Indirect Extrusion Presses: Depending on the specific requirements of the task, these presses can handle varied extrusion processes, offering both standard and reverse extrusion capabilities.
-
Aging Ovens: These are used post-extrusion to accelerate the aging process of aluminum, enhancing its final properties through controlled heat treatment.
-
Precision Cutters: For ensuring exact length specifications, precision cutting tools are employed, providing uniformity across batches.
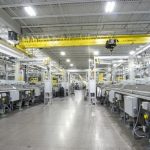
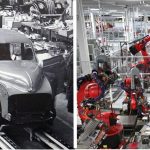
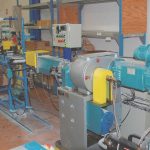
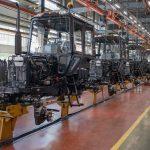
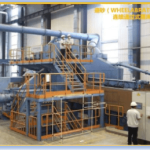
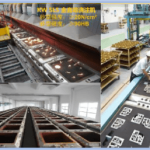
-
Automotive: Aluminum extrusion is vital for creating lightweight, durable components for vehicles, contributing to fuel efficiency and overall performance.
-
Construction: In construction, extruded aluminum profiles are used for structural and design elements, offering durability and resistance to environmental factors.
-
Aerospace: The aerospace industry values extruded aluminum for its strength-to-weight ratio, corrosion resistance, and suitability for complex shapes.
-
Electronics: Thanks to its thermal conductivity and shielding properties, extruded aluminum is widely used in electronic housings and components.
At Promax Engineering, we steer the future of advanced aluminum extrusions with our cutting-edge technology and seasoned expertise. Our dedication lies in meeting precise client specifications with every component, ensuring consistency, durability, and superior quality. By merging technical prowess with relentless innovation, we shape solutions that propel industries forward, marking us as a forerunner in aluminum extrusion services.
Casting is a manufacturing process where a liquid material is poured into a mold containing a hollow cavity of the desired shape, then allowed to solidify. The solidified part, known as a casting, is then ejected or broken out to complete the process. At Promax Engineering, we offer a range of casting methods — including die, sand, and investment casting — to create parts that meet diverse and complex industrial needs.
-
Design Versatility: Casting accommodates complex shapes and designs, including internal cavities and intricacies that would be difficult to achieve with other manufacturing processes.
-
Size Flexibility: The process supports a broad size range, capable of producing tiny components for intricate applications or large parts for heavy-duty uses.
-
Cost-Efficiency: Casting is often more economical for creating complex shapes because it requires fewer secondary machining and fabrication processes. It’s particularly cost-effective for high-volume production.
-
Material Choice: A wide range of metals and materials can be used in the casting process, allowing for specific material properties like durability, strength, and temperature resistance.
-
Furnaces: Used for melting and maintaining molten material before it is poured into molds.
-
Die Casting Machines: These are used for forcing molten metal into molds under high pressure, ideal for high-volume, consistent production runs.
-
Molding Machines for Sand Casting: These prepare the sand molds into which molten metal is poured, used for casting complex shapes.
-
Centrifugal Casting Machines: They use centrifugal force to produce cylindrical parts with a great finish and high material integrity.
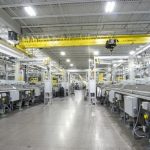
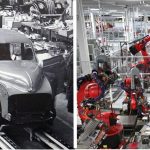
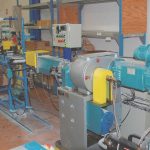
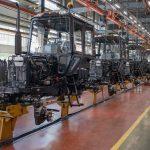
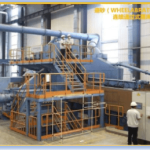
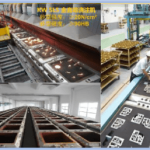
-
Automotive: Casting creates durable, complex components for vehicles, including engine parts, pump housings, and more, contributing to the efficiency and reliability of automotive assemblies.
-
Aerospace: The aerospace industry requires high-strength, precision-made components, often achieved through casting processes to handle extreme conditions effectively.
-
Heavy Machinery: Casting is used to create robust parts for machinery in construction, mining, and other heavy-duty industrial applications, demanding high performance and durability.
-
Consumer Electronics: Precise and aesthetic components for gadgets and consumer electronics are often manufactured using specialized casting methods for detailed design realization.
Promax Engineering takes pride in its sophisticated casting solutions, offering unmatched expertise and technological advances to meet complex industry demands. Our comprehensive casting services are a testament to our commitment to quality, precision, and customer satisfaction. We ensure each cast component adheres to the highest standards, enhancing the operational integrity of the applications they serve, and driving progress across various industries.
Casting is a manufacturing process where a liquid material is poured into a mold containing a hollow cavity of the desired shape, then allowed to solidify. The solidified part, known as a casting, is then ejected or broken out to complete the process. At Promax Engineering, we offer a range of casting methods — including die, sand, and investment casting — to create parts that meet diverse and complex industrial needs.
https://wp.promaxeng.com/wp-content/uploads/promax-1-convert.mp4
-
Design Versatility: Casting accommodates complex shapes and designs, including internal cavities and intricacies that would be difficult to achieve with other manufacturing processes.
-
Size Flexibility: The process supports a broad size range, capable of producing tiny components for intricate applications or large parts for heavy-duty uses.
-
Cost-Efficiency: Casting is often more economical for creating complex shapes because it requires fewer secondary machining and fabrication processes. It’s particularly cost-effective for high-volume production.
-
Material Choice: A wide range of metals and materials can be used in the casting process, allowing for specific material properties like durability, strength, and temperature resistance.
-
Furnaces: Used for melting and maintaining molten material before it is poured into molds.
-
Die Casting Machines: These are used for forcing molten metal into molds under high pressure, ideal for high-volume, consistent production runs.
-
Molding Machines for Sand Casting: These prepare the sand molds into which molten metal is poured, used for casting complex shapes.
-
Centrifugal Casting Machines: They use centrifugal force to produce cylindrical parts with a great finish and high material integrity.
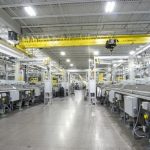
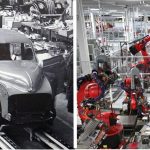
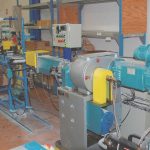
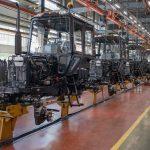
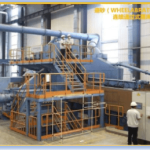
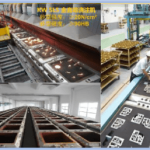
-
Automotive: Casting creates durable, complex components for vehicles, including engine parts, pump housings, and more, contributing to the efficiency and reliability of automotive assemblies.
-
Aerospace: The aerospace industry requires high-strength, precision-made components, often achieved through casting processes to handle extreme conditions effectively.
-
Heavy Machinery: Casting is used to create robust parts for machinery in construction, mining, and other heavy-duty industrial applications, demanding high performance and durability.
-
Consumer Electronics: Precise and aesthetic components for gadgets and consumer electronics are often manufactured using specialized casting methods for detailed design realization.
Promax Engineering takes pride in its sophisticated casting solutions, offering unmatched expertise and technological advances to meet complex industry demands. Our comprehensive casting services are a testament to our commitment to quality, precision, and customer satisfaction. We ensure each cast component adheres to the highest standards, enhancing the operational integrity of the applications they serve, and driving progress across various industries.
Unwavering Quality Commitment
At Promax Engineering, quality isn’t just an assurance; it’s woven into the fabric of our operations. Our commitment to excellence is uncompromising, merging seasoned expertise with continuous innovation to deliver parts that stand the test of time and performance.
Cost-Effectiveness Meets Excellence
Navigating the balance between affordability and high-quality can be challenging. At Promax, we’ve transformed this balancing act into an art. We ensure our clients receive the exceptional value they deserve, coupling affordability with superior quality.
Join Us on the Road to Excellence
Your journey towards manufacturing excellence begins with Promax Engineering. Discover how our capabilities can drive your success in the automotive sector, transcending expectations and redefining standards.